Key Takeaways
- New tariffs and expiring tax provisions are affecting U.S. manufacturers.
- There's a significant trend towards reshoring, driven by supply chain disruptions, trade policies, and governmental incentives.
- Manufacturers need to reinvigorate their supply chain strategies by focusing on import locations, manufacturing centers, and product design.
Rising costs, supply chain disruptions, and logistical challenges have plagued the manufacturing industry for years. But now, tariff changes, trade policies, and technology shifts are creating a state of chaos.
Cargo volumes at various U.S. ports are expected to be elevated over the next few months as tariffs go into effect. And cross-border transportation and supply chain logistics are straining under the changing landscape.
According to our 2025 Mid-Market Manufacturing Outlook, manufacturers are facing the following challenges.
The Impact of Tariffs and Taxes
Tariffs are typically used to help the U.S. compete more effectively in the international marketplace. The administration’s goal is to keep companies from sourcing products overseas and shift manufacturing production, one-third of all imported manufacturing inputs originate in North America and 56% of goods imported to the U.S. are considered manufacturing inputs.
Couple this with the fact that many of the provisions from the Tax Cuts and Jobs Act are scheduled to expire at the end of 2025, and it’s no wonder manufacturers are feeling pressure.
Though the impact of these new tariffs and changes is unclear, proactive planning and supply chain optimization can prepare manufacturers for success. Here’s what you need to consider.
Proactive Planning: Reshoring versus Offshoring
One noticeable trend is reshoring. The global supply chain disruption caused by COVID-19 initiated this change as the industry dealt with shipping delays and increased costs. Companies began to consider reshoring – bringing manufacturing and production back to the United States.
The trend continues today, with 69% of manufacturers reshoring at least part of their supply chain, due to trade policies, tariffs, taxes, and other government initiatives.
However, this is not a decision to make quickly. Factors like cost, taxation, technology, risk mitigation, and workforce are all key drivers. Before committing to reshoring, it’s important for manufacturers to think proactively — and long term — about their organization and its needs. After all, strategic domestic supply chain investments can take years to plan and develop.
Things to consider include:
- How and where are your products being sourced?
- How are your products being distributed?
- How will a location change impact your organization?
How will your location impact your organization?
Geographic location plays a significant role in matters such as international expansion or bringing operations back to the U.S. Factors like currency, tax structures, and other considerations are influenced by the physical area where your company operates.
Implications to consider include:
- Corporate income tax
- Individual taxation, including payroll
- State and local tax
- A variety of tax credits and incentives for sustainable buildings in the U.S.
- Workforce availability
- Proximity to suppliers
- Read more: Key Considerations for Global Expansion
Reinvigorate Your Supply Chain Strategy
Supply chain is a constant topic of conversation, with over half of mid-market manufacturers citing supply chain disruptions as a top concern. For many, this includes rising transportation costs (41%), supplier issues (39%), limited transparency (21%), and transportation and logistics disruptions (21%).
Based on the fluctuating circumstances, we encourage clients to focus on three specific areas when looking into their supply chain:
- Import locations: Where will you place your centers of distribution?
- Manufacturing: Will you move your manufacturing center to the U.S.? How will you source materials and equipment?
- Design: How will you design your products? What types of facilities will you need? Are you adding new products or service lines that are U.S. based?
By mapping your global supply chain, you can gain an understanding of all processes, stakeholders, locations, and activities that will be impacted.
The Impact of Data
Here’s the reality: these decisions can only be made with strong data. Manufacturing leaders must prioritize data across the supply chain to ensure data that is instant, accessible, and reliable.
Digitization of the supply chain is critical for visibility. Our study found that 33% of manufacturers are working to digitize their supply chain processes and 45% are optimizing inventory management strategies.
This kind of integrated, transparent data helps with:
- Forecasting future shifts based on market fluctuations, inventory levels, and seasonal shifts.
- Assessing rising costs and improving demand planning and forecasting.
- Gaining stronger visibility into supply chain monitoring factors like production service rate, lead time, and inventory turn.
Prioritizing Operational Efficiency
There’s a lot to consider when it comes to potentially changing course as a manufacturer. In addition to taxation, the impact of technology is critical. Our study found that over 90% of mid-market manufacturers feel ready to embrace smart manufacturing.
And it makes sense. A digitally optimized manufacturing facility can reduce manual tasks and shorten equipment downtime. AI tools and automation can speed up traditional processes and allow manufacturers to future-proof their operations.
According to HLB’s Business Leader Survey, over 60% of companies aim to improve operating efficiencies this year. This focus enhances transparency, output, and productivity.
Better expense forecasting, product costing, and inventory tracking can boost profitability and help manufacturers predict future impacts. This agile strategy prioritizes productivity and growth over maintaining inefficient systems.
When this level of visibility is present, manufacturers can:
- Renegotiate products or contracts.
- Review and implement profitability and cash management planning, including transfer pricing analysis.
- Research investment in new manufacturing products or warehouse properties.
What’s Next
One thing is certain — the uncertainty will continue. And while you might not be able to predict what new trade policies or legislative shifts are coming, you can take strategic, proactive steps to be prepared.
Manufacturers who routinely review their processes, digitize their supply chain, and keep an eye toward efficiency will be ahead of the competition going forward.
After all, every organization deserves to realize its full potential. And we help our manufacturing clients do just that every day. Let us help you prepare for the now — and the next.
2025 Mid-Market Manufacturing Outlook Report
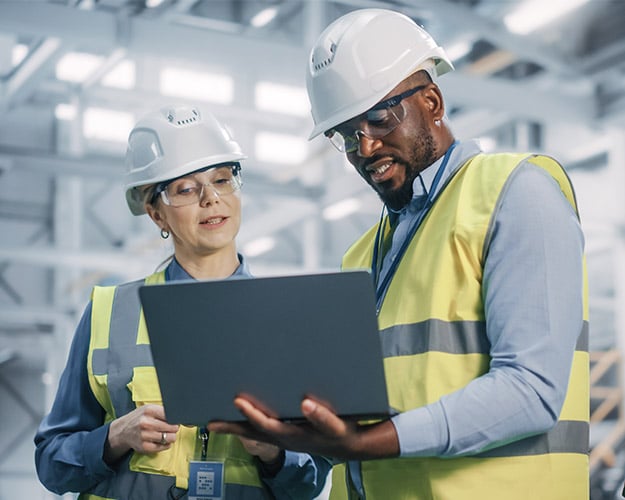
Manufacturing, Distribution, and Logistics
Rely on the trusted expertise of manufacturing advisors to help you build and execute your strategic vision.