Key Takeaways
- Outdated technology and legacy systems can be significant barriers to recruitment, retention, and productivity.
- Younger generations expect employers to provide modern, user-friendly tools that support efficiency and eliminate manual tasks.
- Advanced tools like ERP systems, AI, IoT devices, and robotics enable manufacturers to improve operational efficiency, reduce manual work, and empower employees to focus on strategic, high-value tasks.
Labor constraints are pushing manufacturers to rethink how they recruit, hire, train, and retain their valued workforces. This shift is also driven by generational differences, especially younger generations' evolving expectations around work, work-life balance, and technology. Today’s employees want to work with more modern tools that support productivity, eliminate manual tasks, and make them more efficient.
Manufacturers want to attract and retain the best people, and the best people want to work for modern organizations that leverage technology efficiently.
Manufacturers that rely on outdated enterprise resource planning (ERP) software and other core business systems may struggle to attract and retain top talent. These legacy systems tend to lack the modern, user-friendly interfaces and automation capabilities that employees increasingly expect to use for daily projects and tasks.
Retaining top talent will be extremely difficult for manufacturers relying on manual, inefficient processes to run their operations. Instead of prioritizing strategic projects, those manufacturers may find themselves playing catch-up and putting out fires stemming from outdated technology.
- Learn more about how to optimize your workforce for peak financial and operational performance.
By upgrading or replacing their current technology systems, organizations can help meet modern workforce needs while improving their efficiency, productivity, competitiveness, and profitability.
Untethering from Manual, Time-Consuming Work
To offset the persistent labor shortage, attract new candidates, and raise retention rates, smart manufacturers are turning to modern technology tools — which also provide benefits like real-time production visibility, better resource utilization, earlier identification of potential bottlenecks, and other actionable predictive insights that help improve operational efficiency.
According to our recent survey report, the top tools manufacturers are using to achieve these goals include:
After all, legacy systems and manual processes don’t support growth. When skincare manufacturer and distributor Skin Script was struggling with inventory management, financial planning, and agility, we helped them implement a custom solution that allowed them to scale and triple their volume without needing to hire, add space, or upgrade their technology.
”The increase in efficiency is really impacting our operations. It’s more than I anticipated.”
Tim Chapman, Shipping Warehouse Manager | Skin Script
In short, employees don’t want to spend their time buried in spreadsheets and manual data entry. When equipped with the advanced tools they need, employees can do their jobs more efficiently, reducing the time spent on tasks and freeing up valuable human capital to focus on higher-value tasks.
2025 Mid-Market Manufacturing Outlook Report
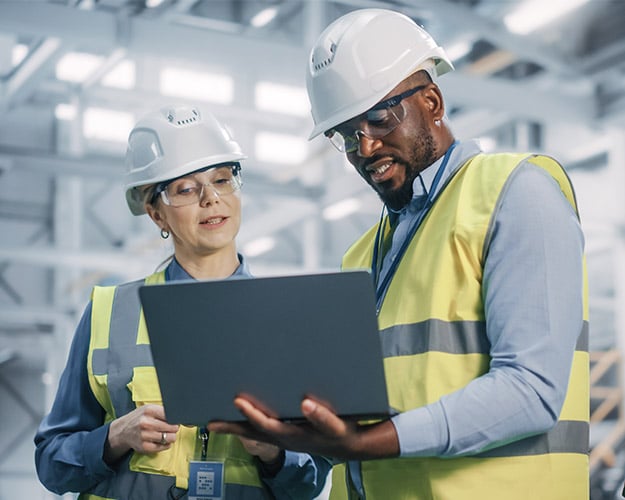
Manufacturing, Distribution, and Logistics
Rely on the trusted expertise of manufacturing advisors to help you build and execute your strategic vision.
Who We Are
Eide Bailly is a CPA and business advisory firm helping our clients grow, thrive, and embrace opportunities and innovation.
